98% Digital Traceability Achieved Through Tamper-Proof Laser Marking – ROI in Just 6 Weeks
Executive Summary
A Tier 1 manufacturer of turbine blades was facing a rising number of Suspected Unapproved Parts (SUP) and tightening certification requirements. By implementing deep-engraved, tamper-proof laser marking directly in the final finishing cell, each component received a unique and immutable Data Matrix code. The result: end-to-end traceability (+35 PP), 30% fewer non-conformances, and a 92% reduction in inspection time. The investment paid off within just six weeks.
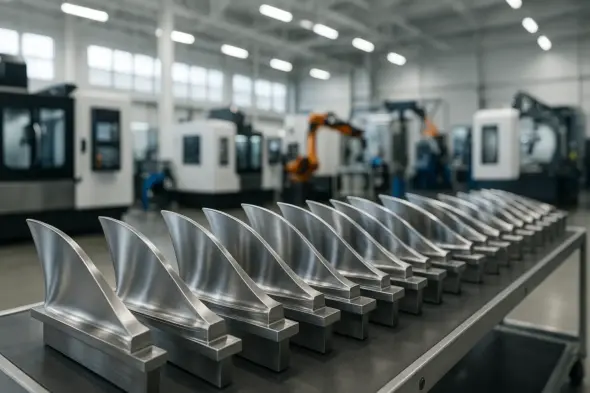
Context / Persona
- Company: Tier 1 supplier of safety-critical structural and engine components
- Role: Head of Quality & Regulatory Compliance (AS9100 / EASA Part 21 G, Part 145)
- Objectives: Eliminate counterfeit parts, minimize certification risks, reduce process costs
Challenge
- Problem scope: The FAA estimates that 2% of the 26 million aircraft parts installed annually—roughly 520,000 components—are either counterfeit or unapproved.
- Regulatory pressure: AS9100 Rev D explicitly mandates documented processes to prevent counterfeit parts (Clause 8.1.4).
- Technical gap: Labels, ink, and surface-level engravings cannot withstand shot peening, coatings, or MRO chemicals—traceability fails exactly when it’s most critical.
Solution Approach
Deep engraving (≥ 100 µm): Code can only be destroyed through material removal – ensuring physical protection against counterfeiting.
A “digital birth certificate”: Unique ID links each part to batch, CoC (Certificate of Conformity), and Form 1 documentation.
Invisible micro-engraving enables secondary (forensic) authenticity checks.
< 8 seconds cycle time, automatic handover to MES/PLM and SUP database.
No heat-affected zone with optimized parameters; resistant to oxidation and corrosion.
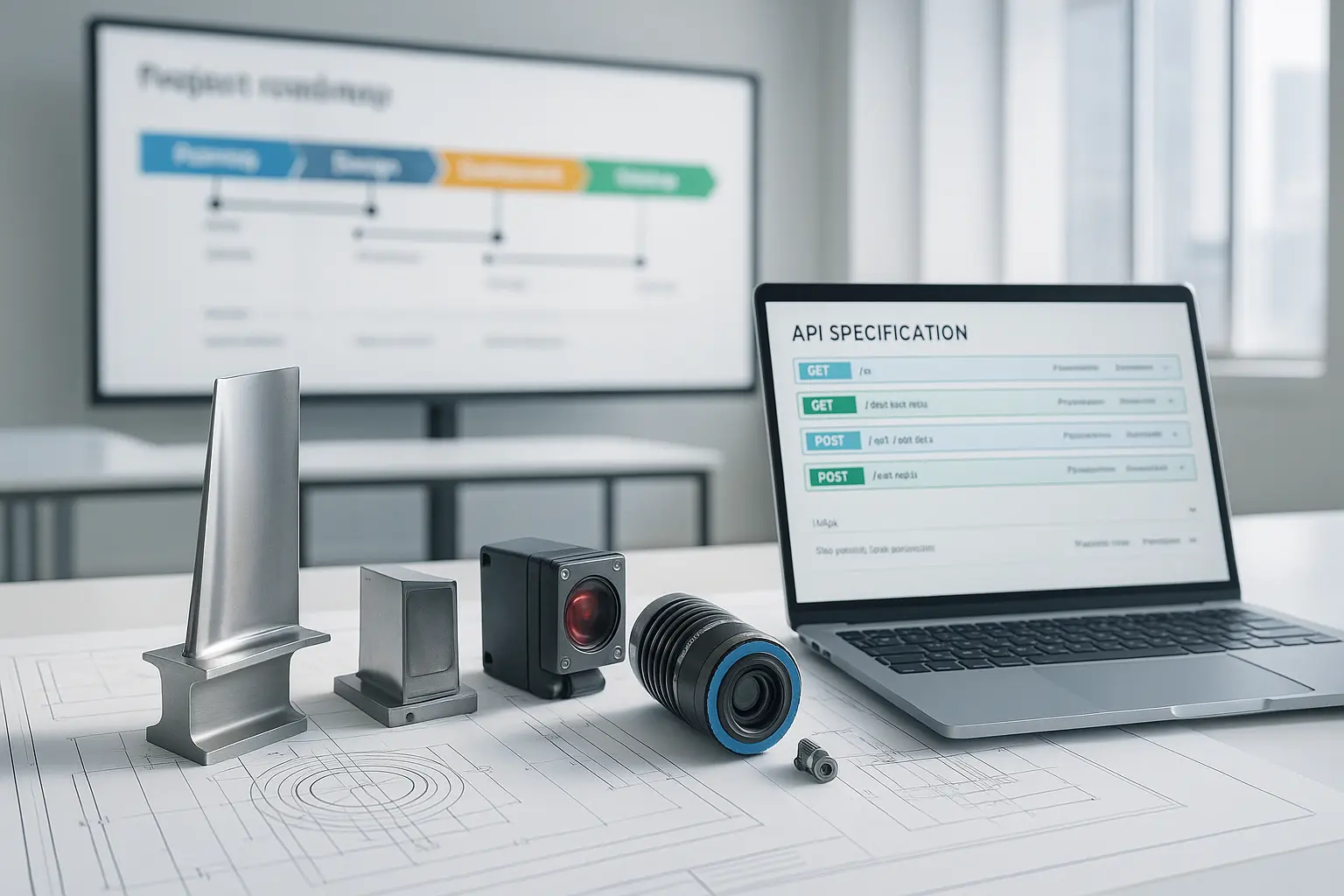
Implementation Roadmap
Phase | Duration | Stakeholders | Effort |
---|---|---|---|
Requirements & Specifications | 1 week | Quality, Production, IT | Workshop |
Pilot Installation (Laser + Vision) | 2 days | Production Engineering | ½ day downtime |
MES/ERP Interface (REST API) | 2 weeks | IT, Senodis | Parameter testing |
Operator & QA Training | 3 days | QA Team | SOP update |
Audit Run & Rollout | From Week 4 | Quality, Certifiers | Real-time monitoring |
KPIs
Digital Traceability
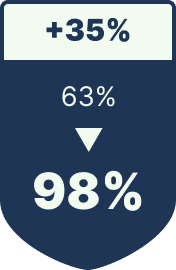
Non-Conformance-Rate
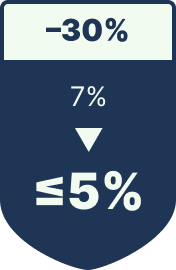
Scrap (Finished Parts)
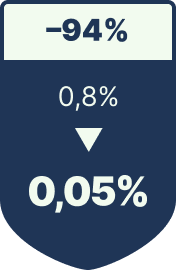
Inspection Time “Part Origin”
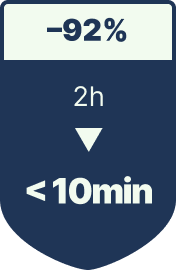
(Key Performance Indicator, delta, baseline, result)