Steel bar production
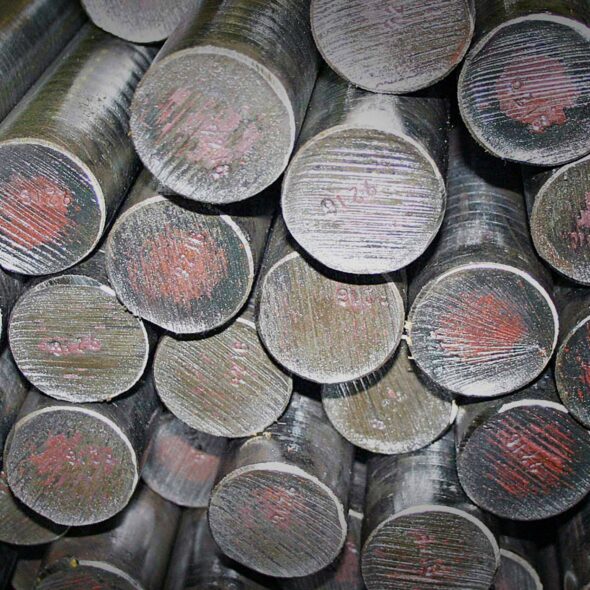
Challenge
In the production of steel bars, an application in the field of massive forming, rolled steels are separated while hot. The surface temperature after separation is still over 300 °C. After separation, the bars are cooled and bundled. Without appropriate labelling, the bars must then be assigned to their original material batches using complex procedures in order to prevent material mix-ups.
Consequences of a lack of labelling are:
- Risk of confusion due to missing assignment to material batches
- Lack of traceability
- Missing assignment of process data
- Limited quality control
- Manual assignment and transfer of material and test data
Use Case: Component traceability
CeraCode® marking on each component Scanning of the respective parts and precise localisation Part-specific release possible Scanning of the respective parts and precise localisation
When switching from series processes to batch processes, when separating large semi-finished products or in processes with severe deformation or high process temperatures, it is often impossible to guarantee reliable allocation. With our Track & Trace solutions, consisting of the right labelling solution and an intelligent camera system, components can be tracked even through harsh and confusing processes.
- No material mix-ups
- Labelling of hot surfaces
- Simple integration
Use Case: Automatic data transfer
CeraCode®-marking on each component Part-specific release possible Scanning of the respective parts and precise localisation Detection of quality deviations
Process, product and test data are not only used for internal quality assurance, but must also be regularly exchanged with partners. This data must neither fall into the wrong hands nor be transferred in the wrong volume. With our additional modules, we guarantee secure and reliable data transfer between our customers and their partners.
- Secure and sovereign data transfer
- Direct transmission without centralised cloud storage
- Simple integration into existing systems
Use case: Internal Q control solid forming
CeraCode® marking on each component Scanning of the respective parts and precise localisation Part-specific release possible Detection of quality deviations
Tests during series production are elementary pillars of quality assurance. From time to time, specification deviations occur that call the component quality into question. In order to avoid mixing with good parts and to be able to precisely limit errors, we support you with modern track and trace solutions.
- Precise defect containment
- Reduction of components to be scrapped
- Reduction of the scope of sorting measures